金属プレス加工の基礎
金属スタンピングは、平らな金属シートを特定の形状に変換するために使用される製造プロセスです。これは、ブランキング、パンチング、曲げ、ピアシングなど、多数の金属成形技術を含む複雑なプロセスです。
自動車、航空宇宙、医療、その他の市場の産業に部品を提供する金属スタンピング サービスを提供する企業は世界中に何千もあります。世界市場が進化するにつれて、複雑な部品を迅速に大量に生産する必要性が高まっています。
次のガイドでは、金属プレス設計プロセスで一般的に使用されるベスト プラクティスと公式を示し、部品にコスト削減の考慮事項を組み込むためのヒントが含まれています。
スタンピングの基本
スタンピング (プレスとも呼ばれます) では、平らな金属シートをコイルまたはブランクの形でスタンピング プレスに配置します。プレスでは、工具と金型の表面が金属を目的の形状に成形します。パンチング、ブランキング、曲げ、コイニング、エンボス加工、フランジ加工はすべて、金属を成形するために使用されるスタンピング技術です。
材料を形成する前に、スタンピングの専門家は CAD/CAM エンジニアリング技術を使用してツールを設計する必要があります。これらの設計は、各パンチと曲げが適切なクリアランスを維持し、最適な部品品質を維持できるようにできる限り正確でなければなりません。1 つのツールの 3D モデルには数百のパーツが含まれる場合があるため、設計プロセスは非常に複雑で時間がかかることがよくあります。
ツールの設計が確立されると、メーカーはさまざまな機械加工、研削、ワイヤー放電加工、その他の製造サービスを利用してその生産を完了できます。
金属プレスの種類
金属スタンピング技術には、プログレッシブ、フォースライド、ディープドローの 3 つの主要なタイプがあります。
順送金型スタンピング
順送金型スタンピングには多数のステーションがあり、それぞれに独自の機能があります。
まず、ストリップ金属が順送プレス機に供給されます。ストリップはコイルから着実に広げられてダイプレスに入り、そこでツールの各ステーションが異なる切断、パンチ、または曲げを実行します。後続の各ステーションのアクションが前のステーションの作業に追加され、その結果、パーツが完成します。
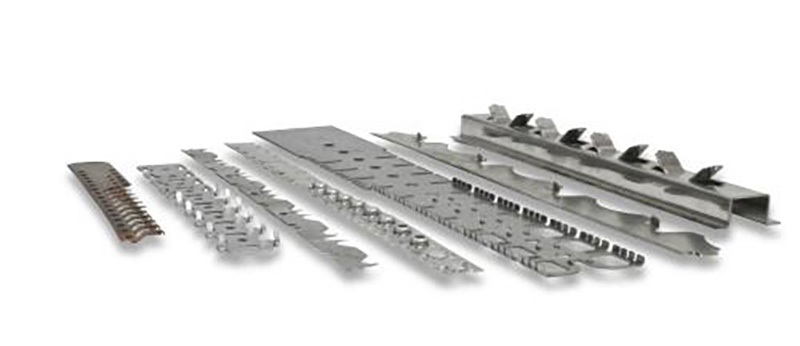
メーカーは、1 台のプレス機で工具を繰り返し交換したり、複数のプレス機を占有して、それぞれのプレス機で完成部品に必要な 1 つのアクションを実行したりする必要がある場合があります。複数のプレス機を使用する場合でも、部品を完全に完成させるには二次加工サービスが必要になることがよくありました。そのため、順送金型スタンピングは次のような用途に最適なソリューションです。複雑な形状の金属部品会うために:
- より迅速なターンアラウンド
- 人件費の削減
- ランレングスが短い
- より高い再現性

フォースライドスタンピング
フォースライド、またはマルチスライドには、水平方向の位置合わせと 4 つの異なるスライドが含まれます。言い換えれば、4 つのツールを同時に使用してワークピースを成形します。このプロセスにより、複雑な切断や複雑な曲げが可能になり、最も複雑な部品の開発も可能になります。
Fourslide メタル スタンピングには、従来のプレス スタンピングに比べていくつかの利点があり、多くの用途にとって理想的な選択肢となります。これらの利点には次のようなものがあります。
1.より複雑な部品にも対応できる汎用性
2.設計変更に対する柔軟性の向上
その名前が示すように、フォースライドには 4 つのスライドがあります。つまり、スライドごとに 1 つずつ、最大 4 つの異なるツールを使用して複数の曲げを同時に実現できます。材料がフォースライドに送り込まれると、ツールが装備された各シャフトによって材料が次々と曲げられます。
深絞りスタンピング
深絞りでは、板金ブランクをパンチを介して金型に引き込み、形状を形成します。絞り加工の深さがその直径を超える場合、この方法は「深絞り」と呼ばれます。このタイプの成形は、複数の一連の直径を必要とするコンポーネントの作成に理想的であり、通常より多くの原材料を使用する必要がある旋削プロセスに代わるコスト効率の高い代替手段です。深絞りで作られる一般的な用途と製品には次のようなものがあります。
1.自動車部品
2.航空機部品
3.電子リレー
4.器具および調理器具
深絞りスタンピング
深絞りでは、板金ブランクをパンチを介して金型に引き込み、形状を形成します。絞り加工の深さがその直径を超える場合、この方法は「深絞り」と呼ばれます。このタイプの成形は、複数の一連の直径を必要とするコンポーネントの作成に理想的であり、通常より多くの原材料を使用する必要がある旋削プロセスに代わるコスト効率の高い代替手段です。深絞りで作られる一般的な用途と製品には次のようなものがあります。
1.自動車部品
2.航空機部品
3.電子リレー
4.器具および調理器具
ショートランスタンピング
短期間の金属スタンピングでは、事前の工具費用が最小限で済むため、プロトタイプや小規模プロジェクトには理想的なソリューションとなります。ブランクが作成された後、メーカーはカスタム ツール コンポーネントとダイ インサートの組み合わせを使用して、部品を曲げたり、穴を開けたり、穴あけしたりします。カスタム成形操作と小さな実行サイズにより、1 個あたりの料金が高くなる可能性がありますが、工具コストがかからないため、多くのプロジェクト、特に迅速な納期が必要なプロジェクトでは、短期実行の方がコスト効率が高くなります。
スタンピング用の製造ツール
金属スタンピングの製造にはいくつかのステップがあります。最初のステップは、製品の作成に使用される実際のツールを設計および製造することです。
この初期ツールがどのように作成されるかを見てみましょう。ストックストリップのレイアウトとデザイン:設計者は、ストリップを設計し、寸法、公差、送り方向、スクラップの最小化などを決定するために使用します。
工具鋼およびダイセットの機械加工:CNC は、最も複雑な金型であっても、より高いレベルの精度と再現性を保証します。5 軸 CNC ミルやワイヤーなどの機器は、非常に厳しい公差で硬化工具鋼を切断できます。
二次加工:金属部品には熱処理が施され、強度が向上し、用途に対する耐久性が向上します。研削加工は、高い表面品質と寸法精度が必要な部品の仕上げに使用されます。
ワイヤー放電加工機:ワイヤ放電加工は、帯電させた黄銅線の素線を用いて金属材料を成形します。ワイヤ EDM は、小さな角度や輪郭など、最も複雑な形状を切断できます。
金属プレスの設計プロセス
金属スタンピングは、ブランキング、パンチング、曲げ、ピアッシングなどの多数の金属成形プロセスを含む複雑なプロセスです。ブランキング:製品の大まかな輪郭や形をカットする工程です。この段階では、部品のコストを押し上げ、リードタイムを延長する可能性があるバリを最小限に抑え、回避することが重要です。このステップでは、穴の直径、形状/テーパー、エッジから穴までの間隔を決定し、最初のピアスを挿入します。

曲げ:打ち抜き金属部品に曲げを設計するときは、十分な材料を考慮することが重要です。曲げを実行するのに十分な材料があるように部品とそのブランクを設計するようにしてください。覚えておくべきいくつかの重要な要素:
1.穴に近づけて曲げると変形する恐れがあります。
2. ノッチとタブ、およびスロットは、材料の厚さの少なくとも 1.5 倍の幅で設計する必要があります。これ以上小さくするとパンチに力が加わり、作成が困難になり、破損の原因となります。
3.ブランクデザインのすべての角には、材料の厚さの少なくとも半分の半径が必要です。
4.バリの発生と深刻さを最小限に抑えるために、可能な限り鋭い角や複雑な切り抜きを避けてください。このような要因が避けられない場合は、スタンピング時に考慮できるように、デザインのバリの方向に必ず注意してください。
鋳造:この動作は、打ち抜き金属部品のエッジを叩いてバリを平らにしたり壊したりするときに行われます。これにより、部品形状の鋳造領域に非常に滑らかなエッジを作成できます。これにより、部品の局所的な領域にさらなる強度を加えることができ、バリ取りや研削などの二次プロセスを回避するために利用できます。覚えておくべきいくつかの重要な要素:
塑性と結晶粒方向– 可塑性は、力を受けたときに材料が受ける永久変形の尺度です。可塑性が高い金属ほど成形が容易です。結晶粒方向は、焼き戻し金属やステンレス鋼などの高強度材料では重要です。強度の高いものの木目に沿って曲げると、亀裂が発生しやすくなります。
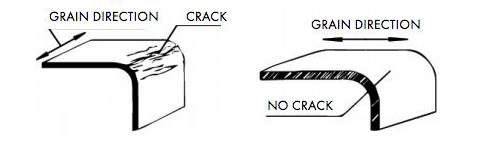
曲げ歪み/膨らみ:曲げ歪みによって生じる膨らみは、材料の厚さの 1/2 に達する場合があります。材料の厚さが増加し、曲げ半径が減少すると、歪み/膨らみはより深刻になります。搬送ウェブと「不一致」カット:これは、部品に非常にわずかなカットインまたはバンプアウトが必要な場合で、通常は深さが約 0.005 インチです。この機能は、複合またはトランスファータイプのツーリングを使用する場合には必要ありませんが、順送金型ツーリングを使用する場合には必要です。
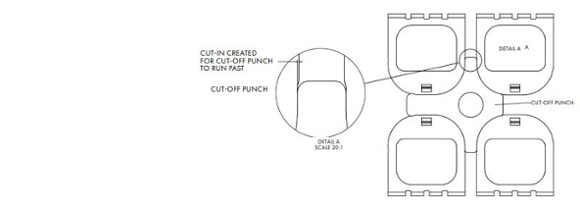
医療業界のバイタルモニタリング機器用のカスタムプレス部品
医療業界の顧客は、医療分野で重要な監視機器のスプリングや電子シールドとして使用される部品のカスタム金属スタンプを依頼してきました。
1.彼らはスプリングタブ機能を備えたステンレススチールボックスを必要としており、妥当なスケジュール内で手頃な価格で高品質のデザインを提供してくれるサプライヤーを見つけるのに苦労していました。
2.部品全体ではなく、部品の一端のみにめっきをしたいというクライアントの独自の要求に応えるために、高度なシングルエッジの選択めっきプロセスを開発できる業界トップの錫めっき会社と提携しました。
MK は、一度に多くの部品ブランクを切断できる材料積層技術を使用して、複雑な設計要件を満たすことができ、コストを制限し、リードタイムを短縮しました。
配線およびケーブル用途向けの打ち抜き電気コネクタ
1. 設計は非常に複雑でした。これらのカバーは、床内および床下の電気配線路内でデイジーチェーン ケーブルとして使用することを目的としていました。したがって、このアプリケーションには本質的に厳しいサイズ制限がありました。
2.顧客の仕事の中には、完全に完成したカバーを必要とするものもあれば、そうでないものもあったため、製造プロセスは複雑で高価でした。つまり、AFC は部品を 2 つの部分から作成し、必要に応じてそれらを溶接していました。
3. サンプルのコネクタ カバーとクライアントから提供された 1 つのツールを使用して、MK のチームは部品とそのツールをリバース エンジニアリングすることができました。ここから、150 トンの Bliss 順送金型スタンピング プレスで使用できる新しいツールを設計しました。
4.これにより、クライアントが行っていたように 2 つの別々の部品を製造するのではなく、交換可能なコンポーネントを備えた 1 つの部品を製造できるようになりました。
これにより、大幅なコスト削減が可能になり、500,000 個の部品を注文した場合のコストの 80% オフとなり、リードタイムも 10 週間ではなく 4 週間になりました。
自動車エアバッグ用のカスタムスタンピング
自動車顧客は、エアバッグに使用する高強度、耐圧性の金属グロメットを必要としていました。
1. 34 mm x 18 mm x 8 mm の絞りでは、グロメットは 0.1 mm の公差を維持する必要があり、製造プロセスは最終用途に固有の固有の材料の伸びに対応する必要がありました。
2. グロメットはその独特の形状のため、トランスファー プレス ツールを使用して製造することができず、その深絞りには独特の課題がありました。
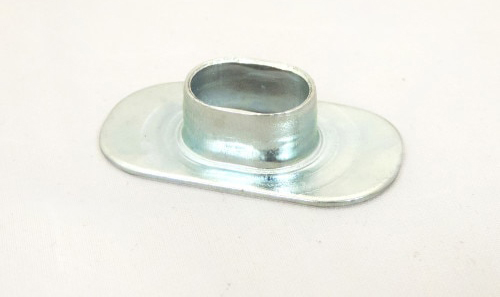
MK チームは、絞りを適切に開発するために 24 ステーションのプログレッシブ ツールを構築し、最適な強度と耐食性を確保するために亜鉛メッキを施した DDQ 鋼を使用しました。金属スタンピングは、幅広い業界向けの複雑な部品の作成に使用できます。当社が取り組んできたさまざまなカスタム金属スタンピング アプリケーションについて詳しく知りたいですか?ケーススタディのページにアクセスするか、MK チームに直接連絡して、専門家と独自のニーズについて話し合ってください。